端子台の教科書®
端子台(端子盤)とは
端子台について
端子台とは、「電気を使う装置」と「電線」を接続するための部品です。電線の接続方法には、主にねじで締めるものが多いです。用途としては電力を各装置に送る、電気信号を分岐させるなどがあります。他にも高圧な電流を扱う場合に分岐点(端子台)を設けることにより故障や事故のリスクを減らす目的もあります。使用される場面は電気を使用する装置であれば必ずといっていいほど使用されることが多いです。
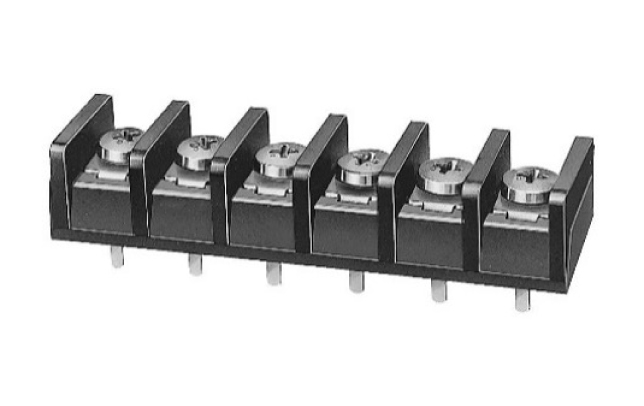

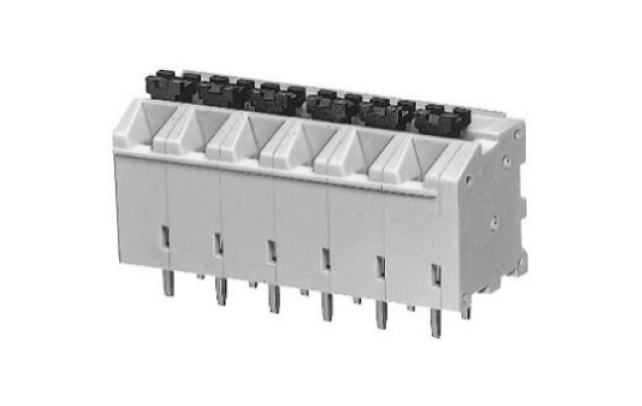
接続方法について
接続方法は一般的なねじ締めの他にもプッシュイン式、タブ式、または当社が開発を行った瞬結式など様々です。又、端子台自体の取付けは、ビスによる固定または、DINレール取付が主流でした。しかし、現在では、プリント基板に直接取り付け、はんだ付けによって固定される端子台も各種作られています。プリント基板用ではコネクタ構造部分をプリント基板に直接接続できる「コネクタ型端子台(当社名称:コネクタンシ)」もございます。これらは、NECA C 2811で「工業用端子台」として定義されています。
-
ねじ式
電線(圧着端子)を端子ねじにて導電部に締付けて接続する。
-
ねじアップ式
電線(圧着端子)電線を端子ねじにて導電金具に締め付けて接続する。ねじを緩めるとバネの力でねじが浮き上がる。ねじが抜け落ちることが無く結線作業の省略化に繋がる。
-
押締式
端子ねじを回転させることで電線押付金具と導電金具が電線を挟み込むことで接続される。
-
タブ式
電線をリセクタブル端子に接続しタブに差し込み電線を接続する方法。
-
ねじ無し式(プッシュイン式)
電線(単線・より線又は、棒・フェルール端子)をクランプバネのバネ圧で導線部に押し付けて接続する。抜く時はノブを押してバネを開口させる。工具フリー(電線加工除く)で結線が可能となる。
-
瞬結式
圧着端子を挿入するとレバーが立ち上がりバネが圧着端子を押さえることにより結線が可能となる。抜く時はレバーを下ろすことで可能。工具フリー(電線加工除く)で結線が可能となる。
端子台ができるまで
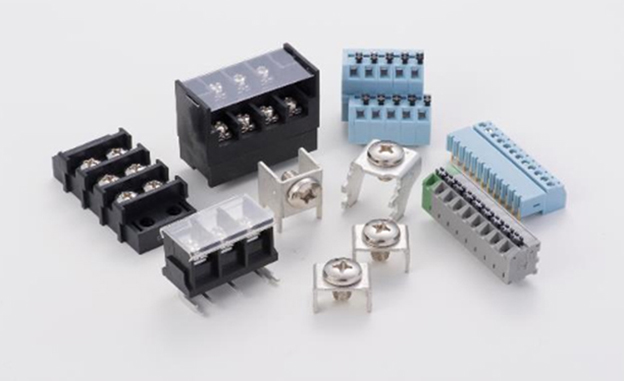
端子台はその多くが「樹脂部品」と「金具部品」から成り立っています。
そして大きく分けて4つの工程が存在します。
1.開発設計
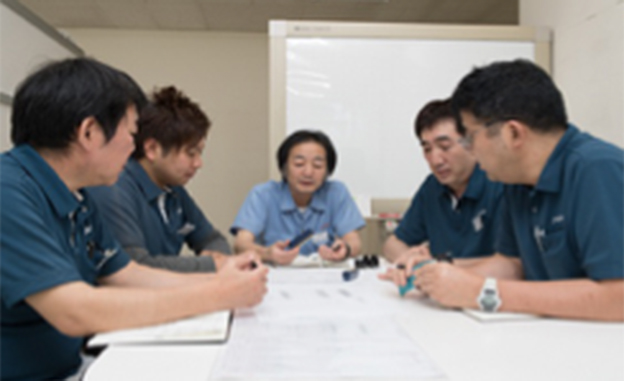
お客様の要望や市場ニーズを基に製品の設計を行います。部品の圧入、組立に必要な治具も設計します。ある程度形状が決まった段階で、試作品を製作、評価を繰り返し完成度を高めます。また試作にあたって近年では3Dプリンターで試作品を作るケースが多くなっています。
2.部品の製作
お客様より注文が入り次第、必要な部品を製作します。主に「樹脂部品」と「金具部品」があり、それぞれ製作方法が異なります。
2.1樹脂部品の製作
樹脂部品の製作に必要なのは、大きく分けて材料、部品の形状を作る金型、部品を作る機械の3つです。大まかな手順としては、材料を溶かしたものを型に注ぎ込み、それが冷えて固まり、硬い樹脂部品になるというものです。一般に「射出成型」と呼ばれます。
材料はペレットと呼ばれるビーズ状の粒です。製品の色・材質に合わせたペレットを使用します。
次に金型ですが、金型は熱や圧力に耐えられるよう金属製で、内部に製品形状の空洞ができるように作られています。大きな製品になると、型だけで500kgになる事もあります。
これらを『成型機』と呼ばれる機械にセットします。成型機は溶かした材料を圧力をかけながら金型に注ぎ、部品の形状を作る機械です。こうして樹脂部品が作られます。
2.2金具部品の製作
金具部品を作るのに必要なものは、材料、部品の形状を作る金型、部品を作る機械の3つです。樹脂部品と違う点は、材料を金型で打ち抜きながら形を作り、それを繰り返すことで最終的な形状ができるというものです。一般に「プレス加工」と呼ばれます。
材料は金属の板で、ロール状若しくは板状のものを使用します。材料には種類がいくつもあり(黄銅やリン青銅、鉄、ステンレス等)、使用場所に応じた材料を使用します。金型は、部品を打ち抜く圧力に耐えられるよう金属製で、内部に部品形状を作るために必要なピンや刃が並んでいます。これらをプレス機と呼ばれる機械にセットします。プレス機は型を上下方向から繰り返しプレスすることで、セットされた材料を順々に打ち抜いたり、折り曲げたりして形を作り出していきます。(順々に加工するプレスは順送型プレスと呼ばれる)
また、金属部品は形が出来上がった後、メッキと呼ばれる表面処理を行うことが多く、このメッキをすることで錆を防いだり、電気の流れをスムーズにすることができます。
3.組立作業
最終的に製品として販売するには、出来上がった樹脂部品・金具部品を組み立てなければなりません。
製品によって組み立て方は様々ですが、当社で最も多いのは、樹脂部品に金属部品を圧入し、それにねじを付けて完成、となります。
4.検査・梱包・出荷
完成した製品はご注文されたお客様のもとに送られますが、送る前に必要不可欠なのが、製品の検査です。
検査は図面を基にした寸法検査や、キズやカケを確認する外観検査を行います。他にも製品ごとに必要な個所があれば、適切な検査を行います。
検査を合格した製品は、適した大きさの「小箱」に梱包されます。
同じお客様から複数の製品の注文があった場合は、大きめの箱に複数の製品をまとめて梱包していきます。
箱の中にはエアクッションなどを入れ、輸送中の破損を防止するようにしています。
こうして、端子台はお客様のもとに送られます。
端子台の種類、使用用途
①中継型端子台
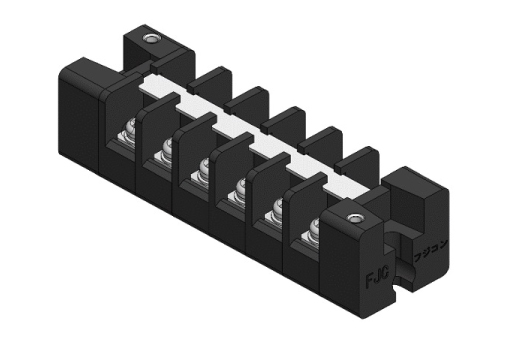
電線同士を手前、奥側2つのねじに結線することよって導通させる端子台。中央のマーカーにより配線内容が一目で確認できる。
用途としては医療器向けを始めとし、工作機器、大型サーボアンプ、レーザー溶接機、電力関係、船舶関係、鉄道関係、防衛関係などへの納入実績が多くあるシリーズ。
②貫通型端子台
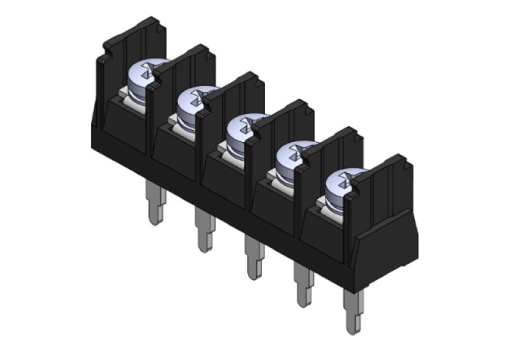
電線をねじで結線し、端子台下部の突出した導電金具に電線を直接はんだ付けしたり、予めプリント基板に設けた挿入穴に挿し込みはんだ付けを行い導通させる。
用途としてはプリント基板に実装される機器の入出力部へ使用。
(主にユニット電源や計測機器に使用)
③貫通型端子台(上下ビス付き)
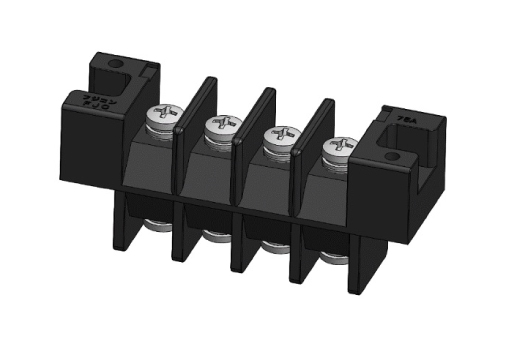
貫通型端子台の上下の結線方法がねじ締めタイプとなった端子台。
用途としては大電流が必要な機器での使用が多い。
④貫通型端子台(二段型)
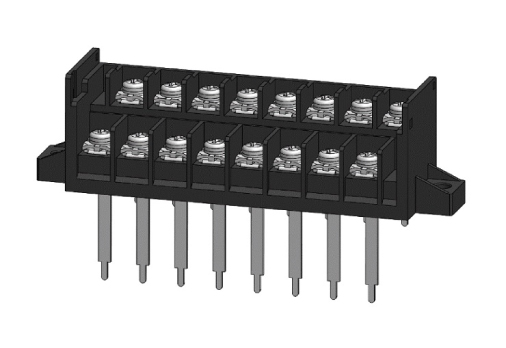
貫通型端子台が二段に分かれたタイプの端子台。二段に増えたことで、より多くの分岐配線が可能となる。
用途としては小スペースに多く配線を行う場合の使用に適している。
⑤コネクタンシ
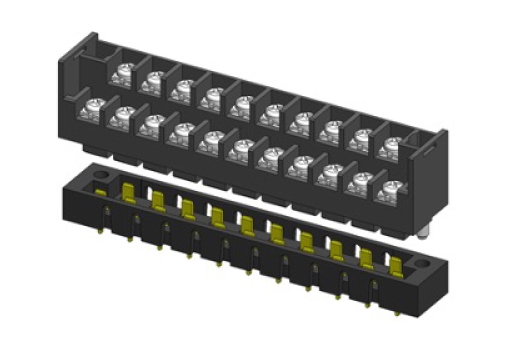
上下で端子台が分かれており、配線後に端子台の着脱が可能な端子台。結線方法は貫通型端子台と共通。
用途としては制御機器向けで開発・販売を行っているシリーズとなっており、着脱できることで使用用途が増えた製品。
⑥基板端子
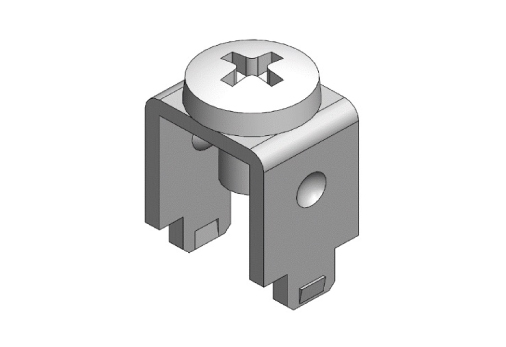
電線をねじで結線し、予めプリント基板に挿入穴を設けてその穴に挿し込みはんだ付けを行うことにより導通させる。
用途としては車載、空調、新エネルギー関係を中心に幅広く使用実績あり。当社標準品でも売れ筋上位シリーズとなっています。
⑦トランジスタクリップ
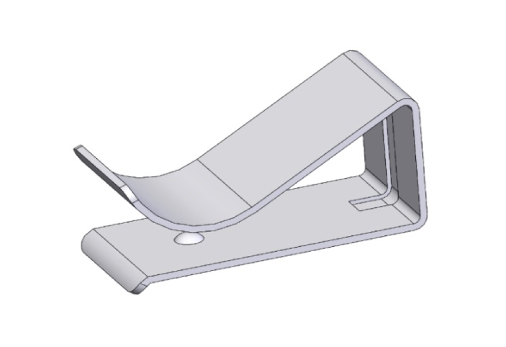
トランジスタを固定するためのもの用途としてはパワコン、電源、放送関係、医療関係、その他トランジスタを使用するあらゆる機器に搭載実績有り。
⑧カスタム品
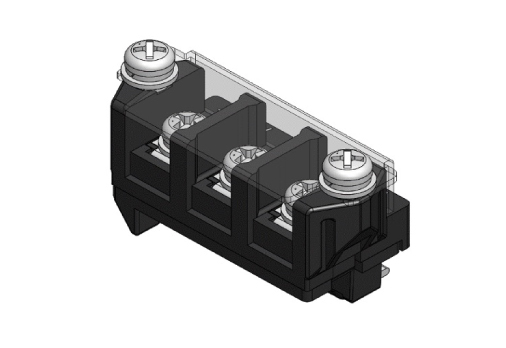
多くのお客様と共に培った技術力を活かし、お客様のご要望に柔軟に対応。樹脂成形品、金具(ブスバー)などのカスタム対応も可能。
端子台に使用するねじについて
1.そもそもねじとは?
ねじの活用方法として、一般的なのは物と物を連結させることです。
またねじの役割の強みは、連結したものを緩める事ができることです。連結させるだけなら、様々な加工法がありますが、ねじは外すことで部分ごとに修理点検、リサイクルに繋げることができます。
2.使用するねじの種類
単体
ねじ頭部の下にねじ山しかないタイプ。
主に基板端子に多く採用されています。(バインドが多い)
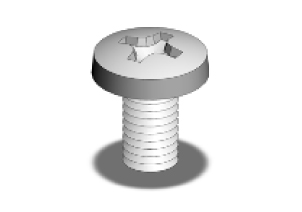
PW座金組み込みねじ(セムスねじ)
ねじ頭部の下に平ワッシャーが組み込まれているタイプ。
セムスねじとは座金組み込みねじと呼ばれる締結部品を指す。カバー止めに多く採用されている。
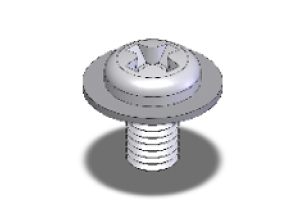
SWセムス
ねじ頭部の下にスプリングワッシャーが組み込まれているタイプ。
タブやショートピースを取り付ける際に多く採用されている。
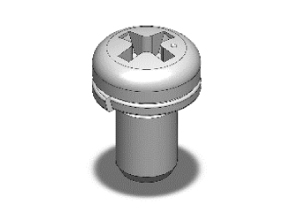
PSWセムス
ねじ頭部の下に平ワッシャーと、スプリングワッシャーが編み込まれていて、最も一般的なビス。(なべ、バインドどちらにも多く採用されている。)
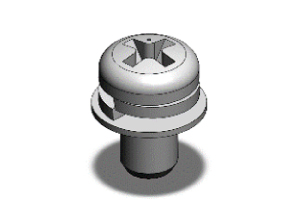
フリー端子ねじ(スパックなし)
ナベ小ねじと、四角形の角座金でできている。鉄ビスが多く磁石にくっつき、作業性の向上が見込めます。
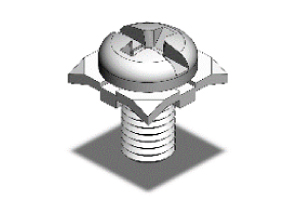
フリー端子ねじ(スパックあり)
ナベ小ねじと四角形の角座金でできている。スパックは、波形状になっているため、スパックなしに比べてばね性が高くゆるみ止めの効果があります。
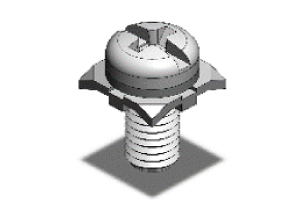
※上記補足
- ねじ頭
- ねじ頭とは、ドライバーを当てる丸い個所を指します。
- なべ
- ねじ頭の形状が鍋のような丸みを持ったねじを指します。
- バインド
-
ねじの頭が台形のような形。なべねじよりも頭の径が大きい。
バインド小ねじは頭部が台形で上面が丸くなっており、ナベ小ねじに比べて少しだけ頭部の径が大きい特徴。締結した部材の陥没や座面を防ぐ目的がある。見た目の違いでも使用されることがある。
- ねじ山
- ねじ頭部から、下螺旋状箇所を指す。ねじ山とねじ山の間隔をピッチといい、ねじサイズによって間隔は異なります。
- セムス
- ねじ頭部の下に、平ワッシャーかスプリングワッシャー、もしくは両方が組み込まれていて、ビスから外れない構造のねじを指す。
- スパック
- スパックとは、波形ばね座金のことで、波形状によって反発力を大きくし、締結部の圧力が均等に分散されて緩みにくくなる座金です。
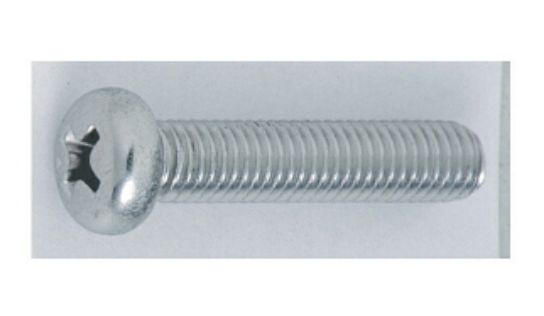
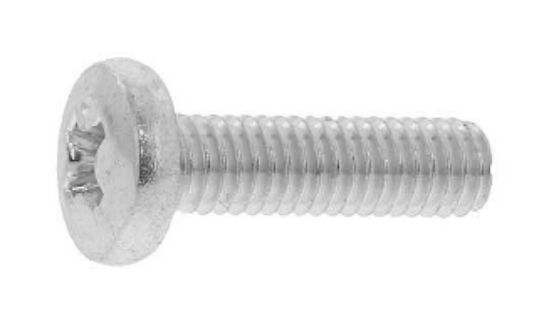
3.ねじにプラスとマイナスがある理由
ねじには、プラスねじとマイナスねじ、そしてプラスマイナスねじの三種が存在します。
これは日本だけの呼び方であり、世界ではプラスねじが「フィリップス」、マイナスねじが「フラット」と呼ばれている。一般的に使用される物の多くが、プラスねじです。今はプラスねじの使用量が9割以上とされ、プラスねじはドライバーにきれいにフィットし、強く押し込むことができるが、汚れがたまりやすく、ねじ穴がつぶれると、使用できなくなる。マイナスは汚れがたまりにくくねじ穴がつぶれることはありませんが、ドライバーとのフィット感がいまいちなことで、強く締め付けることが難しいとされています。
※右にスワイプすると全てご覧になれます
メリット | デメリット | |
---|---|---|
プラスねじ | 十字型 回転軸からねじへ真っすぐ力を伝えることが可能で、締付強度が増す。 | 構造上さびやすい。ねじ穴がつぶれる原因に繋がる。つぶれると取り外しに手間がかかる。 |
マイナス ねじ |
ー字型 汚れにくく、何度締めてもねじ穴がつぶれにくい。ゴミやほこりがたまりやすいが、掃除がしやすい。 | マイナスの溝の為、ドライバーとの相性が悪く、ねじ先がずれやすい。大量生産に向かない。 |
プラス マイナス ねじ |
ねじ頭に十字の切り込みと一次の切り込みがあるため、ドライバーを選ばすに締めることが可能。 | プラス、マイナスねじに比べて少し生産コストがかかる。 |
上記のようなデメリットがありますが、端子台では、結線時のゆるみや安全性を考慮したうえで、プラスねじを使用しています。
4.平ワッシャー、スプリングワッシャーの役割
平ワッシャーの役割は二つあります。1つ目は、部材の陥没を防ぐことで、ねじのゆるみを防止することができます。平ワッシャーを間に挟み、部材に接する表面積を大きくすることで、部材にかかる力が分散し部材の陥没を防ぐことができます。そしてもう一つの役割は、部材を傷つけないようにすることです。平ワッシャーを使わずにねじを強く締めると、部材の材質によっては傷がつきその傷から錆などの劣化につながる場合があります。その他の役割として、食い込み防止、気密性の保持、ゆるみ止め、絶縁、スペーサー等の役割があります。
スプリングワッシャーはばね座金とも呼ばれます。見た目は平ワッシャーと若干似ていますが、ばねの一巻きを切り取ったような形状をしています。
ボルトとナットなどの間に挟んで締め付けると、切り口部分が押さえつけられて変形します。
その時に生じる、反発力により緩み止めとして作用します。
スプリングワッシャーの役割としては、ねじの緩みを防止する事ですが、平ワッシャーとは違い、部材の陥没を防げるわけではありません。通常、スプリングワッシャーを使わずにねじだけで締め付けていると、時間の経過とともにゆるんで来てしまうことが有ります。しかし、スプリングワッシャーを使用して締め付けると、スプリングワッシャーのばね性により、ゆるみを防止する事ができるのです。
※右にスワイプすると全てご覧になれます
役割 | 強み | |
---|---|---|
平ワッシャーとは |
小ねじやボルトなど、締める際、座面と締め付け部の間に入れる部品。 「座面没落防止」、「座面保護」二つの役割を持つ。 |
負荷の力を分散させることに長けている。 |
スプリングワッシャーとは | バネ座金の一部がねじれてビスのゆるみ止め、脱落防止の役割がある。単体でも使用できる。 | 緩み止めに対して、効果がある。 |
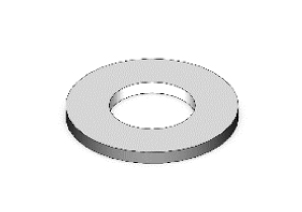
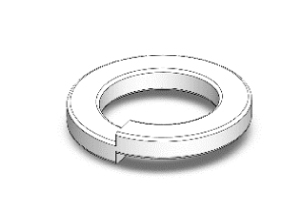
5.表面処理(電気メッキ)について
特徴
電気メッキは電解溶液中に、入れたねじなどを通電し、表面がメッキで覆われるようになります。
用途
電気メッキは装飾以外に防錆、機能など様々な特性を持たせることができます。
表面処理と、塗装や研磨など処理加工を施して素材の表面を仕上げることを指し、処理方法にも、様々な方法がある。メッキ処理もその中の1つとなっている。
メッキ処理の大きな目的としては5つあり
①耐食性をつける
②熱特性をつける
③電気特性をつける
④摩耗性をつける
⑤装飾を施す
メッキ加工の方法
・電気メッキ/電気エネルギーによって溶液中の金属イオンを還元して、導電性のある物体に金属の薄い層を形成させるメッキ法。
※右にスワイプすると全てご覧になれます
特徴・機能 | メッキの種類 |
---|---|
銅メッキ | 銅の展延性に優れる性質により複雑な形状の素材にも均一に被覆できることから下地メッキとして最適である。 ただ変色や腐食を起こしやすいため銅メッキの上にさらにメッキ加工が必要。 |
ニッケルメッキ | 適度な硬度と柔軟性をもち、外観に優れ耐久性がある。 |
亜鉛メッキ | 高い耐食性をもち、鉄に対して密着性が高い。また処理費用が廉価である。 |
クロメート処理 | 主に亜鉛メッキの上から施されることが多く、耐食性の向上や被膜に傷が生じた際には酸化被膜を形成し、金属の腐食を防ぐ。 また光沢を帯びるので外観にも優れる。 |
6.メッキの特性
材質特徴・機能 | 黄銅材 ニッケルメッキ | 鉄材 亜鉛メッキ+クロメート処理 | 鉄材 ニッケルメッキ | 詳細 |
---|---|---|---|---|
耐食性 | ◎ | ○ | × | 鉄材×ニッケルメッキは屋外設置機器には向かない。 |
着磁性 | × | ◎ | ◎ | 鉄材はドライバーのビットを磁性化しておくと、締め作業が容易になる。 |
外観 | ◎ | ○ | ◎ | ニッケルメッキは光沢があり、外観にはわずかながら、優位性がある。 |
イ)耐食性
- 黄銅材 ニッケルメッキ
- ◎
- 鉄材 亜鉛メッキ+クロメート処理
- ○
- 鉄材 ニッケルメッキ
- △
鉄材×ニッケルメッキは屋外設置機器には向かない。
ロ)着磁性
- 黄銅材 ニッケルメッキ
- ×
- 鉄材 亜鉛メッキ+クロメート処理
- ◎
- 鉄材 ニッケルメッキ
- ◎
*「鉄材」は、ドライバーのビットを磁性化しておくとビス締め作業が容易となる。
ハ)外観
- 黄銅材 ニッケルメッキ
- ◎
- 鉄材 亜鉛メッキ+クロメート処理
- ○
- 鉄材 ニッケルメッキ
- ◎
*「ニッケルメッキ」は光沢があり、外観にはわずかに優位性がある。
7.ねじの選び方
以上述べてきましたように、使用される場所、環境、端子台の形状や作業性の重要性などを考慮し、様々なねじの中から最適なものを選択しなければなりません。
ねじの形状や材質、メッキの種類など様々な、物から選ぶには何を優先させるのかを考える必要があります。例えば、事務所などの空調が効いた場所では、使用される環境などは考えず、コストや作業性などを重要視してよいと考える。
逆にねじが錆びてしまうような可能性の高い屋外等で使用されるような場合には、ステンレス製か黄銅材が適していると考えられます。どうしても鉄材を使用したい場合は亜鉛メッキにクロメート処理を施したねじを選択した方が長持ちし、安全性があると言えます。
また、単線を使用する場合などはPSWセムスなどの丸ねじより、フリー端子ねじを使用し、角座金でしっかりと固定することで単線が抜けてしまう危険性を下げることができます。
いずれに致しましても、お客様の要望を優先することはもちろんですが、使用環境を確認し、それに応じた提案やアドバイスをさせていただけましたら、幸いに存じます。
端子台の正しい使い方
正しく使うことで接続機器の性能を十分に発揮できたり、端子台のメンテナンス頻度が下がります。
そしてなによりも事故を未然に防ぐことができます。
端子台には低電圧から高電圧にも耐えうるものが存在し、間違った使用方法によっては重大な事故に繋がる危険があります。
事故を防ぐための適切な使用方法をPDFにてご紹介します。
使用される材料について
モールドなどに使われる樹脂について
熱可塑性樹脂と熱硬化性樹脂の違い
プラスチックには非常に多くの種類が知られていますが、そのどれもが、熱可塑性・熱硬化性のどちらかに分けることが出来ます。熱可塑性とは、熱をかけていくと溶けるチョコレートのようなタイプの樹脂のことで、熱硬化性樹脂とは、熱をかけていくと硬くなっていくクッキーのようなタイプの樹脂です。ただし、熱硬化性樹脂であっても、熱を上げ続けるとある時点で強度が無くなってしまうのでプラスチックを選ぶ際には、この常用できる耐熱温度がどれくらいなのかを念頭に置く必要があります。当社で使用されている樹脂では、熱可塑性樹脂がPBT、PC、PPSなどがあり、熱硬化性ではフェノール樹脂などがあります。
-
当社使用基板(材質:PBT) -
当社使用カバー(材質:PC)
成形材料特徴表
(材質の使用例画像全ての製品に使われているとは限りません)
※右にスワイプすると全てご覧になれます
樹脂名 | 概要 | 特徴 | 用途 | 使用例画像 | |
---|---|---|---|---|---|
PBT | 熱可塑性のエンジニアリングプラスチックの一つで、電気特性をはじめ、各種物性のバランスがよくとれた材質。難燃性の高いグレードも各種販売 ※樹脂名:PBT(ポリブチレンテレフタレート) |
長所 | 耐衝撃性・絶縁性・寸法安定性・耐薬品性 電気的特性など | 電気製品 電子部品 自動車部品など |
![]() |
短所 | 加水分解(恒温恒湿環境下)など | ||||
PC | 熱可塑性のエンジニアリングプラスチックで、無色透明・耐衝撃性・耐候性に優れる材質 ※樹脂名:PC(ポリカーボネート) |
長所 | 耐熱寒性・絶縁性・耐候性・耐衝撃性・透明性など | 電気・電子部品 光学分野 自動車部品 生活用品類など |
![]() |
短所 | 加水分解(恒温恒湿環境下) 耐薬品性など |
||||
PPS | 熱可塑性のスーパーエンジニアリングプラスチックの一つで、剛性の高さが特長。各種物性がハイレベルでまとまっているが、高価 ※樹脂名:PPS(ポリフェニレンサルファイト) |
長所 | 耐熱性・高剛性・電気的特性・耐薬品性・難燃性など | 電気・電子部品 自動車部品 OA機器部品 家電など |
![]() |
短所 | 耐衝撃性(ノッチ効果)・耐摩耗性・高価など | ||||
PF | 熱硬化性プラスチックに分類される、最も古い人工プラスチック。昔はベークライトの名称で作られていた。今でも砥石の基盤として使われることがある。 ※樹脂名:PF(フェノール樹脂) |
長所 | 耐熱寒性・絶縁性・難燃性・耐酸性・耐溶剤性など | 工業用部品 機械的部品 自動車部品 キッチン用品など |
![]() |
短所 | 耐アルカリ性など | ||||
PA | 熱可塑性のエンジニアリングプラスチックの一つ。耐熱性、機械的強度に特に優れている。他にも耐油性や耐.摩耗性、潤滑性に優れている。 ※樹脂名:PA(ポリアミド)ナイロン66 |
長所 | 耐熱性・靭性・耐摩耗性・耐薬品性など | 自動車部品 電気電子部品 食品関連 衣装衣服類など |
![]() |
短所 | 吸水時に寸法変化が生じる 黄変しやすいなど |
||||
POM | 熱可塑性のエンジニアリングプラスチックの一つ。特に潤滑性に優れている。他にも機械的強度に優れている。 ※樹脂名:POM(ポリアセタール) |
長所 | 耐摩耗性・耐衝撃性・自己潤滑性・絶縁性・耐薬品性など | 自動車部品 工業用部品 楽器など |
![]() |
短所 | 対候性・難燃性 |
導電板やビスなどに使われる金属について
当社で使用されている金属は、主に導電性の高い材質を使用しています。また、ほとんどの製品の材料表面に表面処理を行っており、より高い電気的特性を確保しています。 主に使用している材料は銅、黄銅、リン青銅、鉄、ステンレス鋼で、表面処理はニッケルメッキ、スズメッキ、三価クロメートなどがあります。
-
当社使用ビス(材質:鉄) -
当社使用導電板(材質:黄銅)
金属材料特徴表
(材質の使用例画像は全ての製品に使われているとは限りません)
※右にスワイプすると全てご覧になれます
樹脂名 | 概要 | 特徴 | 用途 | 使用例画像 | |
---|---|---|---|---|---|
銅 | 電気・熱の伝導性がよく加工性に優れ、耐食性・耐候性が良い素材。 | 長所 | 電気的特性・熱伝導性・対候性・耐食性・電気的特性など | 電気用、化学工業用の製品・部品 鍋などの調理用品 |
![]() |
短所 | 酸化(錆が発生)し易く、表面処理などが必要な場合がある。 | ||||
黄銅 | 展延性や加工性に優れている素材。一般的に真鍮とも呼ばれる銅と亜鉛の合金で、配合される亜鉛の比率によって特性が変化する。 | 長所 | 電気的特性・熱伝導性・加工性・耐食性など | 端子コネクターなど。 |
![]() |
短所 | 酸化(錆が発生)し易く、表面処理などが必要な場合がある。 | ||||
リン青銅 | 展延性・機械的強度・耐食性に優れ、バネ材に適した素材。銅と錫の合金である青銅にリンを添加して作られる。 | 長所 | 電気的特性・熱伝導性・加工性・耐食性・機械的性質など | 電子・電気機器用ばね、コネクタ、スイッチなど。 |
![]() |
短所 | 酸化(錆が発生)し易く、表面処理などが必要な場合がある。・高価など | ||||
鉄 | 強度・加工性が高く、コストが安い一般的な素材。 | 長所 | 加工性・機械的性質・安価など | 建築、自動車等の部品、ビス、ナットなど。 |
![]() |
短所 | 酸化(錆が発生)し易く、表面処理などが必要な場合がある。 | ||||
ステンレス鋼 | ステンレス鋼とはStain(汚れ)Less(ない)=錆びない(錆びにくい)鋼、という意味で、クロムとニッケルを含有させた合金鋼のこと。耐食性・機械的性質が良好な素材で、錆びにくいという性質を持つ。 | 長所 | 100%リサイクル可能・機械的性質・耐薬品性など | 自動車、電気機器などに使用される板バネ。 |
![]() |
短所 | 吸水時に寸法変化が生じる 黄変しやすいなど |
規格について
規格の必要性
規格(標準)の定義/自由に放置すれば多様化、複雑化、無秩序化する事柄を標準化し少数化、単純化、秩序化することによって制定される「取り決め」。
各規格の位置付け
端子台の適合規格
①IEC(International Electrotechnical Commission)規格
IEC規格は、「国際電気標準会議」という機関が制定する国際規格です。IECは電気通信分野を除く電気・電子分野の広い分野で国際的な標準化を行っています。IECには参加している国は80カ国以上で、日本からは後述するJISを制定する日本産業標準調査会(JISC)が代表として参加しています。
規格は、その規格を制定した団体の種類・規模によって、適用範囲が異なってきますが、ISO(国際標準化機構)やIECといった国際機関が制定した国際規格は全世界で適用されます。
②TÜV規格
TÜV規格はドイツの企業であるTÜV Rheinlandsが制定する規格です。認証企業として、世界7位前後の規模を持ちます。技術、安全、証明サービスの規格を設定し、電気部品の評価方法にはEN(European Norm)規格を利用、評価試験を実施しています。これらの試験に合格した際には、TÜV認証マークの使用が認められています。
EN(European Norm)規格は、欧州30カ国で構成されるCEN(欧州標準化委員会)やCENELEC(欧州電気標準化委員会)、ETSI(欧州通信規格協会)が発行する、欧州の統一規格です。加盟各国は、EN規格を自国の国家規格として採用することが義務付けられています。CEN規格(CEN/CENELEC規格)や欧州規格と呼ばれることもあります。
③JIS(Japanese Industrial Standards)規格
JIS(日本産業規格)とは日本産業標準調査会(JISC)が制定する国家規格です。日本の産業標準化の促進を目的とする産業標準化法(1949年)に基づき制定されました。JISは、産業標準化法に基づく手続きを経て、制定または改正から5年以内に見直しが行われ、当該規格をそのまま存続(確認)、改正または廃止がされます。
JISには、それぞれに番号が付いています。この番号は、分野を表すアルファベット一文字と4桁から5桁の数字との組合せからなります。(1949年以来、長らく日本工業規格として呼ばれてきたが、法改正により2019年7月1日に改称された。)
④UL(Underwriters Laboratories)規格
UL規格は、アメリカ合衆国の企業であるUnderwriters Laboratoriesが制定する規格です。認証企業として、世界10位前後の規模を持ちます。材料・部品・装置・道具類などから最終製品まで、機能と安全性の規格を設定し、同時に評価方法を策定、実際に評価試験を実施します。これらの試験に合格した際には、UL認証マークの使用が認められています。
ULはマークを発行したリストを管理し提供することで、利用者に材料や製品などがUL認定品であるということを提示しています。
⑤NECA(Nippon Electric Control Equipment Industries Association)規格
NECAでは、ISO、IEC等の国際規格の情報収集や調査研究を通じて国際標準化規格の整合化を目指し、国内の審議団体として具体的な提案に結びつける活動を行っています。また、当工業会所管の既存日本産業規格(JIS)の改正や新規JIS規格の制定、並びにNECAの改正や新規制定を行っています。また、端子台に関する規格のJIS C2801の代替規格としてNECA C2811が制定されています。
端子台の主な準拠規格
UL1059 | Terminal Blocks |
---|---|
UL94 | Tests for Flammability of Plastic Materials for Parts in Devices and Appliances. |
JIS C 8201-7-1 | 銅導体用端子台 |
JIS C 2806 | 銅線用裸圧着スリーブ |
NECA C 2811 | 工業用端子台 |
IEC(International Electrotechnical Commission) | 国際電気標準会議 |
![]() |
![]() |
工業用端子台の製品設計について
端子台の基本設計・試験
①当社基本設計
端子台を設計する際は、UL規格のフィールドワイヤリング*1を取得できる構造とする事。また、顧客要求によりフジコン設計基準を外れる場合は、量産性及び品質の検証・確認を行い設計をする事。専業メーカーとして、ユーザーから指示がなくても必要スペックの確認を行い客先へ提案を行う事。
その他、UL1059やNECA C 2811の基準をクリアできる様、注意することを基本姿勢としています。
②設計評価試験
製品開発を行った上で、UL1059やNECA C 2811の基準をクリアしているかどうか試験を行っています。
例えば、耐電圧試験、絶縁抵抗試験、温度上昇試験、締付トルク試験、引張強度試験、耐熱性試験、耐寒性試験、耐湿性試験など各規格の試験方法に則って行い安心してご使用いただけることを確認しています。
*1ファクトリーワイヤリング(FW1)/フィールドワイヤリング(FW2)について
ファクトリーワイヤリング(FW1)とは
端子台を組込んだ機器の端子台への配線を納入先工場内の配電盤内、又は指定された機器のみに制限される規格。規格取得は容易であるが、客先での使用用途が制限されてしまうため、需要が少ない。
フィールドワイヤリング(FW2)とは
端子台を組込んだ機器の端子台への配線を納入先工場の配電盤内、又は指定された機器を含み、外部機器との接続も認められる規格。近年、ほとんどのUL1059取得製品はFW2を要求されています。製品設計を行う際はFW2の規格取得に合わせた設計を行っています。
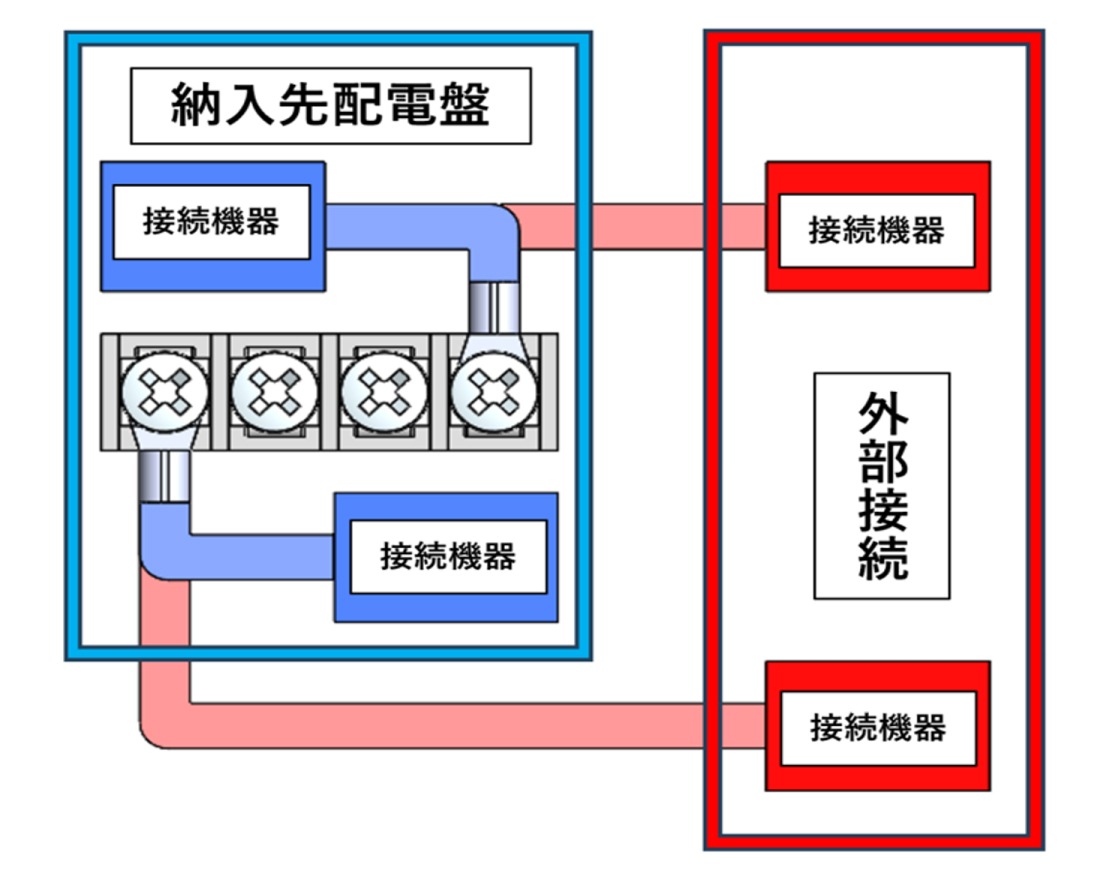
青枠 | 赤枠 | |
---|---|---|
FW1 | ⚪︎ | × |
FW2 | ⚪︎ | ⚪︎ |
工業用端子台(端子盤)の
性能について
「機能」と「性能」の違い
「機能」と「性能」は混同される場合が多いのですが、きちんと使い分けるべき重要な概念となります。 大きな違いは、「機能」とは性質や役割であって、直接数値化できないもの。また、「性能」とは、具体的な指標として数値化できるもの、という表現がわかりすいかと思います。ここでは、そういった数値化した工業用端子台の「性能」について述べていきます。
電気的性能について
①耐電圧
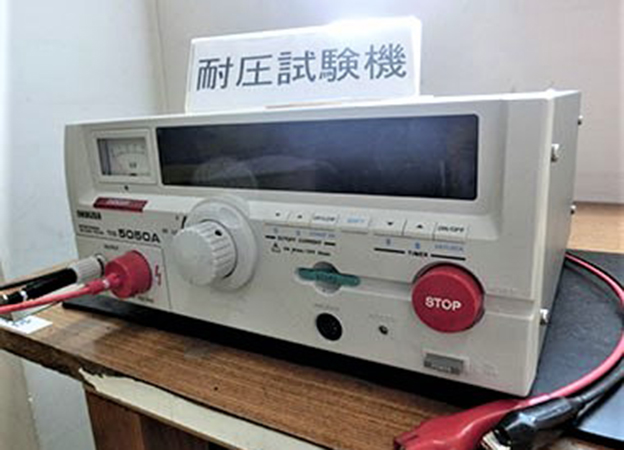
耐電圧試験は、絶縁が確実に施されているかを絶縁部間に高電圧を印加し確認する試験です。また、耐電圧は絶縁破壊を生じることなく確実に印加できる電圧の上限であり、絶縁耐力とも呼ばれます。 準拠規格であるNECA C 2811では、定格絶縁電圧が*250Vの場合は2000Vで、*600Vの場合は2500Vで試験を行うこととなっています。試験方法は、端子台を接地した金属板へ使用状態に取り付け、50Hz又は60Hzの正弦波に近い*上記の電圧で行います。最初に規定電圧値の1/3以下の電圧を加え、以後規定値に達するまで、電圧計を読みながら急速に上昇させます。 印加時間は、電圧が規定値に達した後1分間とします。但し、受渡検査の場合、最初から試験電圧値の120%の電圧を1秒間印加して、これに代えることが出来ます。
②絶縁抵抗
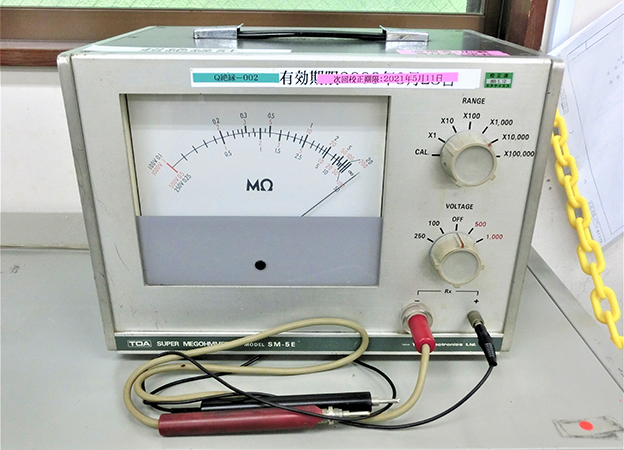
絶縁抵抗とは、電流が流れる電路における電路間及び電路と大地との間の絶縁性(電流が流れない性能)のことです。単位は一般的にMΩ(メガオーム)が用いられます。絶縁抵抗が低くなると漏電を起こし、感電や火災等の原因となるので注意が必要です。
NECA C 2811では、「絶縁抵抗試験は、端子台を金属板へ使用状態に取り付け、500Vの絶縁抵抗計(通称:メガー)を使用し、各充電部相互間、各充電部と取り付け金属板の間の絶縁抵抗を測定する」とありその時の絶縁抵抗は20MΩ以上で無ければならないとされています。当社では、フェノール樹脂のボディで100MΩ、PBT、PET、ポリカーボネートなどのボディで1000MΩ以上と規格より厳しい数値を設定しています。
③温度上昇
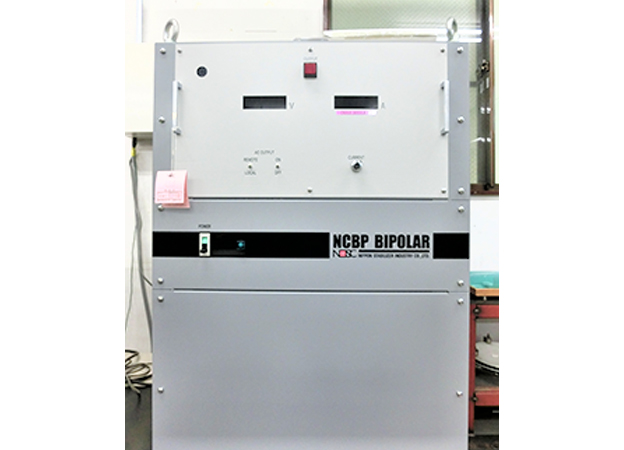
温度上昇試験とは、電子機器の通常作動状態時において、所定の部位(人的接触が可能な部位及び内部にある部品)の温度が規定されている限度温度を超えないかを測定し、火災や火傷などにならないよう製品安全性を評価することを言います。
NECA C 2811に規定された試験方法は、3極以上の端子台にあっては3極、3極以下の端子台にあっては全極を直列に接続し、定格電流を連続して通電し、温度がほぼ一定になった時の中央極の電線接続部に出来るだけ近い部分の温度上昇を熱電対温度計で測定し室温との差異が45℃以下であることとされています。(ULでは30℃以下)
当社は、30℃以下になる設計を基本とし、この条件を満たすように定格や適合電線を決定しています。
環境性能について
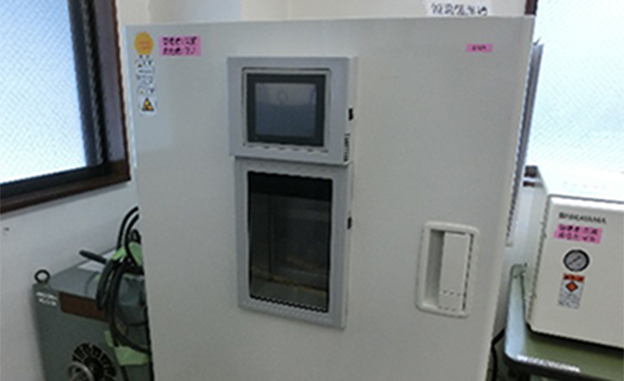
①耐熱性
NECA C 2811では耐熱試験の条件として、「70±3℃の恒温槽に2時間保った後取り出して常温に1時間放置し、異常が無いこと。また、その後耐電圧、絶縁抵抗を測定し、数値が規定を満足すること」とあります。規格より厳しい条件の「120℃」で試験を行っています。
②耐寒性
NECA C 2811では耐寒試験の条件として、「-25±3℃の恒温槽に2時間保った後取り出して常温に1時間放置し、異常が無いこと。また、その後耐電圧、絶縁抵抗を測定し、数値が規定を満足すること」とあります。規格より厳しい条件の「ー40℃」で試験を行っています。
③耐湿性
NECA C 2811では耐湿試験は、「端子台を温度40±2℃、相対湿度90~95%の恒温高湿槽内に96時間保った後、常温・常湿の室内に取り出し、付着した水滴をふき取り、5分以内に耐電圧、絶縁抵抗を測定し、数値が規定を満たすこと」とあります。
当社でもこの規格に基づいた試験を行っています。
機械的性能について
①結線ビスの締付トルク
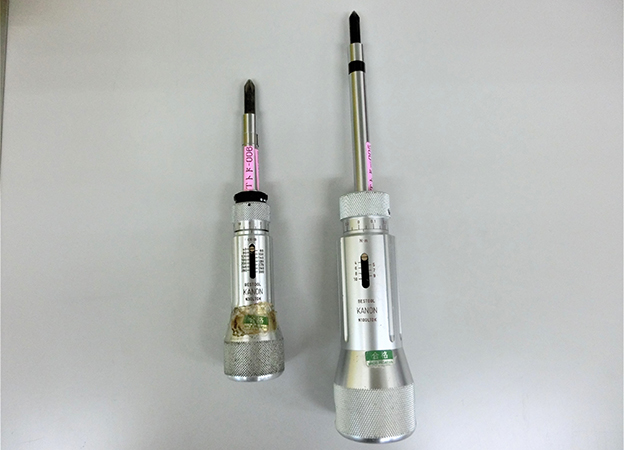
ねじを回して締め付けるときに回転方向にかける力を「締め付けトルク」といいます。ねじを締め付ける時は、締め付けトルクで管理することになります。締め付けトルクが小さすぎるとねじが緩み、締め付けトルクが大きすぎるとねじが破損することになる為です。
NECA C 2811(工業用端子台)では、締め付け強度試験は、端子ねじをトルクドライバなどを使用して徐々に締め付け、表1に示す締め付けトルクを5~15秒間加えた後、端子ねじを緩める、とあります。当社では15秒間と規定し試験しています。
表1(NECA C 2811より) ※備考( )の数値はねじ回し以外の方法で締める場合。
※右にスワイプすると全てご覧になれます
端子ねじの呼び径 mm | 3 | 3.5 | 4 | 5 | 6 | 8 | 10 | 12 |
---|---|---|---|---|---|---|---|---|
締付けトルク N・m | 0.5 | 0.8 | 1.2 | 2.0 | 2.5 | 5.5 | 10.0 | 15.5 |
②導電板(端子部)の引張強度
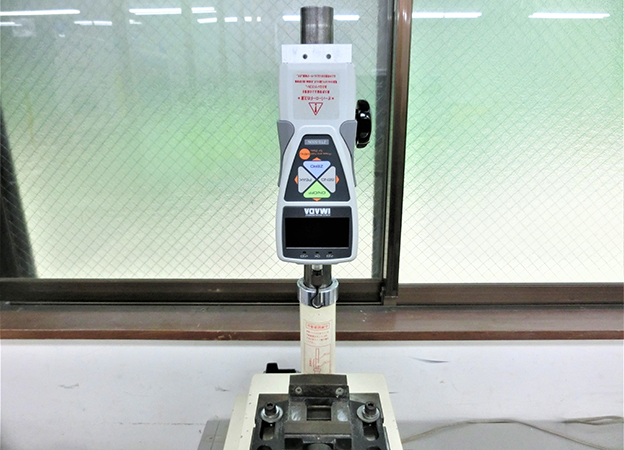
引張強度試験は、端子台に定格適合電線を規定の締付トルクで結線して行います。このとき表2に示す引張力を加え、異常が無いこととしています。ここで導電板が破損してまったり電線が外れてしまったりした異常は危険な為、これも重要な試験であることに間違いありません。
表2(NECA C 2811より)
※右にスワイプすると全てご覧になれます
定格適合電線 | より線 ㎟ | 0.5~1.25 | 2~3.5 | 5.5~8 | 14~22 | 38~60 | 100 | 150 |
---|---|---|---|---|---|---|---|---|
単線 ㎟ | 0.5~1.2 | 1.6~2 | 2.6〜3.2 | 4.1〜5.8 | 6.5〜8.2 | 9.2〜10 | 11〜13 | |
引張力 N | 50 | 100 | 150 | 200 | 250 | 300 | 350 |
③耐振動性
振動試験をする目的は、端子台が取り付けられた後に、周りの機器などの振動による影響により10μs(フジコン規定)以上の電流の断が発生しないことを確認するために行います。(JIS C 5402参照)また、振動負荷による部品のこすれ、傷、破損、あるいはネジの緩みなどによる動作不良などを起こさないか、も確認しています。(NECA C 2811参照)
NECA C 2811の試験方法は以下となっています。
耐振動試験は、端子台を使用状態に取り付け、適当な長さの定格適合電線を、電線接続部の形状に応じた接続方法で接続し、その一端を振動による張力が加えられない程度に固定して行います。
a)振動数範囲と複振幅は、表3に示すいずれかの組合せとする。
b)振動数の速さは、振動数範囲を1往復するのに要する時間が1分の割合とし、連続的でかつ、一様に変化させる。
c)振動を加える方向は、上下、左右及び前後の3軸方向とし、振動を加える時間は、各軸方向共に2時間とする。
表3(NECA C 2811より)
振動数範囲 Hz | 複振幅 mm | ||
---|---|---|---|
10~55 | 0.75 | 1.0 | 1.5 |
- 振動数範囲 Hz
- 10~55
- 複振幅 mm
- 0.75
- 1.0
- 1.5
④耐衝撃性
耐衝撃試験は、端子台を使用状態に取り付け、表4の衝撃を上、下、左、右、前及び後の6方向に各5回、計30回加え破損、変形、変色等の異常の無いこととしています。
表4(NECA C 2811より)
最大加速度 m/s² | 持続時間 ms | 速度変化 m/s |
---|---|---|
500 | 約11 | 3.4 |
- 最大加速度 m/s²
- 500
- 持続時間 ms
- 約11
- 速度変化 m/s
- 3.4
環境負荷物質について
なぜ環境負荷物質はいけないのか
環境負荷物質とは、人の活動が環境に与える影響で、それによって環境の保全に支障が生じる恐れのあるものを言い、その原因となる物質のこと。人の健康や生態系に有害な影響を与える恐れのある物質の為、禁止したり規制が必要となってきている。
フジコンにおいては年に一回、全従業員を対象に環境品質部が主催し、「環境関連教育」「ISO教育」「内部監査教育」などを行っております。その年の業界の状況に合わせて資料を新しく作り直し教育を行っています。
RoHS指令とは
「RoHS指令」は電子・電気機器に使用される危険物質に関する制限のため欧州連合(EU)により2003年2月に公布されました。この指令に基づき、2006年7月1日以降は、EU加盟国内において、RoHS指令の禁止物質の含まれる電子・電気機器を上市することはできなくなりました。
このRoHS指令での環境負荷物質6物質の限界値(閾値)は以下のようになっています。
- 鉛:1000ppm以下
- 水銀:1000ppm以下
- カドミウム:100ppm以下
- 六価クロム:1000ppm以下
- ポリ臭化ビフェニル(PBB):1000ppm以下
- ポリ臭化ジフェニルエーテル(PBDE):1000ppm以下
改正RoHS指令(RoHS2)とは
2015年6月4日、RoHS2の禁止物質(制限物質)にフタル酸系の4物質が追加され、禁止物質は10物質となりました。 改正RoHS指令(RoHS2)は、2011/65/EUのAnnexⅡを置き換える形で(EU)2015/863が公布されました。追加された4物質の限界値(閾値)は以下のようになっています。
- フタル酸ジニエチルヘキシル(DEHP):1000ppm以下
- フタル酸ブチルベンジル(BBP):1000ppm以下
- フタル酸ジブチル(DBP):1000ppm以下
- フタル酸ジイソブチル(DIBP):1000ppm以下